Requirements for guards
As general requirements for guards, important ones include being strong, not causing a new hazard, being difficult to bypass or defeat, not interfering with visibility in the production process to the extent possible.
In addition to these, the requirements below apply depending on the type of guard.
1. Requirements for fixed guards
A fixed guard shall be held in the position to which it was affixed in the following manner:
● Being permanently affixed by welding or other means; or
● Being affixed by screws and nuts so that it can only be removed or opened by the use of tools such as a special screwdriver.
2. Requirements for movable guards
In general, movable guards shall meet the following requirements and shall associate with the control system of a machine as needed:
● Being affixed to a machine or its structure by a hinge or a guide rail not only while they are closed but also while they are open;
● Not allowing an operator to start the moving part of a machine in a case where an operator can reach it.
In addition, after starting the moving part of a machine, an operator cannot reach it. This system can be achieved with the use of an interlocking guard (with guard locking, as needed) among the movable guards; and
● Preventing the moving part of a machine from starting in a case where the guard of a movable guard is shifted from its original position or removed, or devices, including an affixed interlocking device, lack or fail. Alternatively, stop the movable part of a machine if the machine is in operation. This can be achieved through automatic monitoring of a control system.
3. Requirements for interlocking guards with a start function (control guards)
An interlocking guard with a start function is a special form of interlocking guard which, once the guard is closed, automatically starts the machine without the use of a separate start controller (e.g., a start switch). This guard is allowed to implement only when all of the following requirements are satisfied:
● The guard basically satisfies all the requirements as an interlocking guard;
● The machine has a short cycle time;
●The maximum time during which the guard is open is set at a small value (e.g., equivalent to a cycle time)
Once this time has elapsed, the machine cannot be started even if the guard is closed. In this case, a reset is required;
● The machine has the size or shape that ensures that the whole body will move outside a hazard zone (to a safe position) when the guard is closed;
● The interlocking device used for the interlocking guard with a start function is designed to have, for example, a duplexed system and automatic monitoring in order to prevent an unintended start resulting from a failure; and
● The guard can reliably maintain its opened state by means such as a spring or a counterweight to prevent the guard from causing a malfunction and starting the machine while it is descending because of its own weight.
4. Emission reduction
For hazards that were not adequately reduced through inherently safe design measures, including noise, vibration, and hazardous substances (gas/steam), protective measures shall be taken using, for example, a noise suppressor, vibration damping equipment, or the forced ventilation of the relevant area.
Selection and implementation of sensitive protective equipment
Separately from guards, which are physical shields, there are regulations concerning the types and application of sensitive protective equipments. A proper selection shall be made according to the use.
1)Selection and implementation of sensitive protective equipments
Light curtain (active opto-electronic protective device: AOPD (Note))
A equipment that performs a detection function with the photoelectric transmitter and the photodetector that detects a shade of an opaque object existing in a detection area (A type of ESPE (Note), there are Type 2 and Type 4).
Laser scanner (active opto-electronic protective device to diffuse reflection: AOPDDR (Note))
A equipment that detects an object using its photoelectric projector that emits radiation to irradiate an object existing in a predefined two-dimensional detection area and using its photodetector that detects the resulting diffusely reflected light (A type of ESPE, there is a Type 3).
Pressure detection mat
A mat that detects the presence of a human body or an object by sensing changes in pressure (e.g., changes in resistance) acting on the mat when a person steps on the mat.
Trip bar, trip wire
The sensitive protective equipments described above are used for passage detection (trip) of an opaque object like a human body, or for presence detection within a safeguarded space, or for both purposes.
Note) Reference
- ESPE: electro-sensitive protective equipment
This includes light curtains, pressure detection mats, and laser scanners, and performs a protection trip or presence detection.
- AOPD: active opto-electronic protective device
This generally refers to light curtains. A kind of ESPE.
- AOPDDR: active opto-electronic protective device to diffuse reflection
This generally refers to laser scanners . A kind of ESPE.
2) Matters to be considered in using sensitive protective equipments
● Install a sensitive protective equipment at a proper place in such a way that people will not be able to approach a hazard by circumventing the device.
For example, when using a light curtain, install it in such a way that people will not be able to insert, for example, the hand into a hazard through a gap at the upper or the lower part / at the right or the left part by circumventing the optical axes.
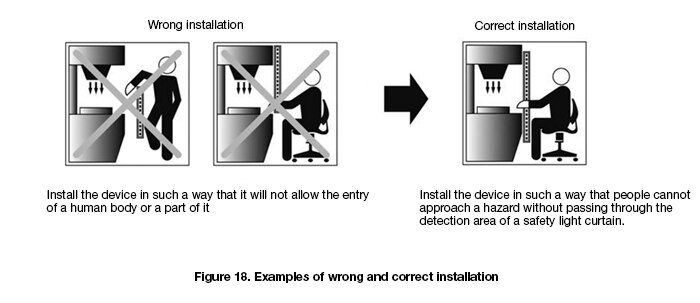
● Create a safety distance between people and a hazard by taking into account the overall stop time required for both the sensitive protective equipment and the machine.
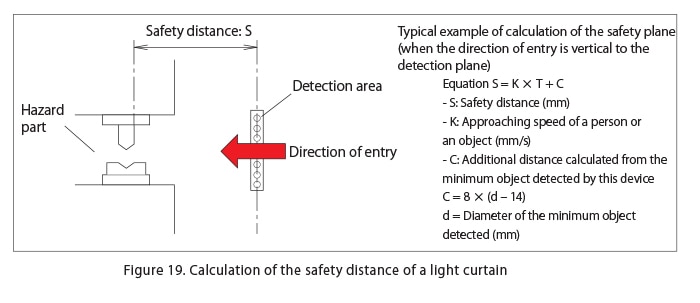
● Sensitive protective equipments shall generate a stop command immediately they detect a person or a part of a human body.
● The exit of a person or a part of a human body from a detection area shall not, by itself, restart the hazard of a machine. In addition, a stop command by a sensitive protective equipment shall be maintained as a system until a next command is given.
● A restart shall be made possible only when an operator intentionally operates a control device (restart switch) located outside a hazard zone.
● Being able to enter into a hazard zone without being detected or being able to be present in a hazard zone shall be prevented. To achieve this, a device may be used with, for example, a fixed guard as needed.
Note that a sensitive protective equipment alone will not suffice in the cases below. Adding protective measures or reviewing the use of a sensitive protective equipment is required.
● A case where substances, such as chips of materials and cutting oil, fly out of a hazard zone
● A case where noise, dust, X rays, etc. are emitted
● A case where there is an irregular long stop time in the middle of a process, which may be misunderstood that the machine is at a complete stop, and
● A case where there is a characteristic that does not allow an emergency stop to be made in the middle of a cycle (where the moving part of a machine has a considerable inertial force).
3) Additional requirements for sensitive protective equipment when used for cycle initiation
There are exceptional cases where the exit of a person or a part of a human body from the detection area of a sensitive protective equipment may automatically restart a cycle of a machine primarily to improve productivity. This, however, is subject to various conditions and requirements. For details, see the text of ISO12100.
Even after risk reduction is achieved, complimentary protective measures could have to be implemented as required by the intended use and reasonably foreseeable misuse of a machine. Complimentary protective measures have the following five typical examples:
● Providing a machine with an emergency stop function so that the machine can be immediately stopped by human intention to avoid a pressing emergency situation;
● Means of escape for a person caught in a machine, and means of rescue for cases where escape is impossible;
● Means of complete interruption of power (e.g., electric power) and means of eliminating energy that is accumulated inside, in preparation for maintenance and other occasions;
● Measures for safe handling of heavy objects including machines; and
● Measures that ensure safe approach or access to the relevant part of a machine.
Emergency stop function
- Actuators, including an emergency stop switch (e.g., mushroom push-button), shall be clearly recognizable and quickly accessible for operation.
- When an emergency stop command is given by pressing, for example, an emergency stop switch, the machine shall be stopped as promptly as possible without creating a new hazard.
- An emergency stop command shall be maintained until it is reset (the machine maintains the stopped state).
- Resetting an emergency stop command (resetting an emergency stop switch) shall only be possible at the place where that command was given.
- Resetting an emergency stop function shall not restart the machine but shall only allow a restart.
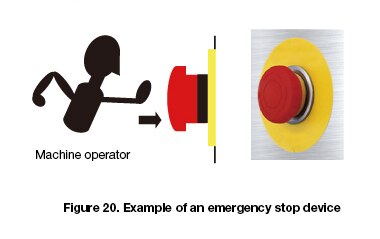
Measures for the escape and rescue of trapped persons
- escape routes and shelters in installations generating operator-trapping hazards,
- arrangements for moving some elements by hand, after an emergency stop,
- arrangements for reversing the movement of some elements,
- anchorage points for descender devices,
- means of communication to enable trapped operators to call for help.
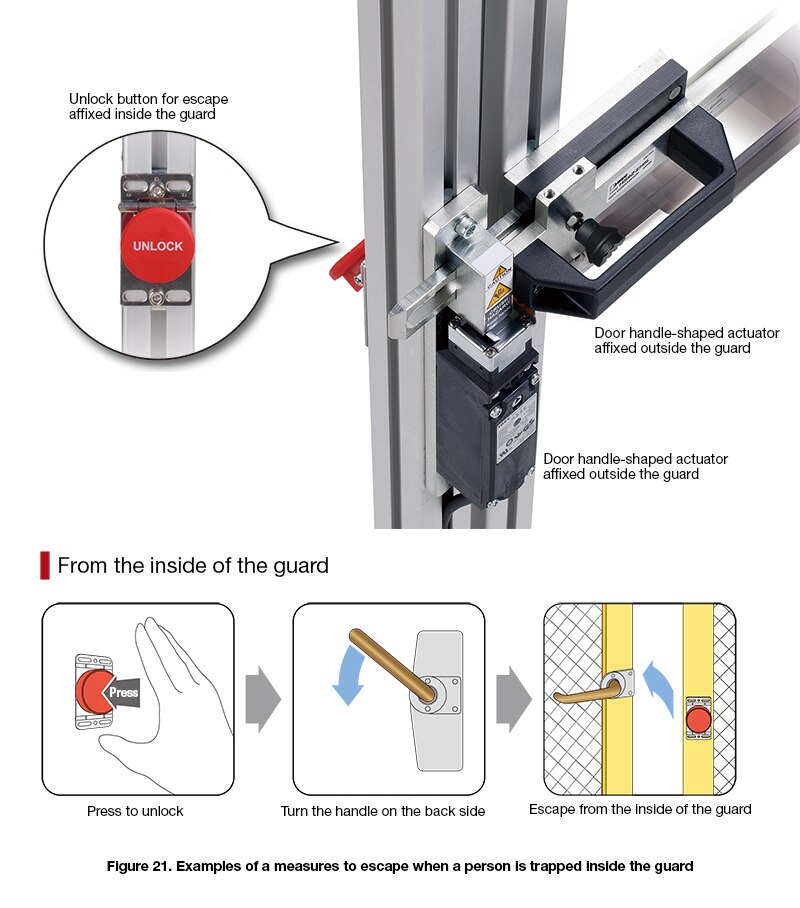
Measures for isolation and energy dissipation
● Being able to disconnect and separate a machine (or a relevant part) from power supply.
● Being able to lock the position of “Isolation” with a padlock or by other means in all isolating units.
● Eliminating stored energy that can cause a hazard, or if that is not possible, contain it.
Provisions for easy and safe handling of machines and their heavy component parts
Heavy machines shall be equipped with a device that facilitates transport by lifting gear or shall allow a device for transport to be safely attached to it.
● Being equipped with lifting tools that have slings, hooks, eyebolts, or tapped holes for appliance fixing.
● Being equipped with fork locating devices for machines to be transported by a lift truck.
Measures for safe access to machinery
● Machinery shall be designed so that every work can be performed on the ground level to the extent possible. In case this is not possible, provide means of a safe approach such as a platform or a staircase.
● Means of approaching an elevated spot of machinery shall provide protective measures against a falling accident (e.g., a staircase, a ladder, a safety enclosure of a ladder, mooring tools necessary to protect from a fall).
● Make walking areas with non-skid materials.
● Design/place control devices, including switches attached on a panel surface, in such a way that they will not be stepped on and used as an aid to an approach.
A risk, which resides after taking inherently safe design measures as well as safeguarding and complimentary protective measures, shall be clearly communicated to users of the machine as Information for use.
Information that shall be communicated include each of the stages related to the operation of the machine, such as transport, assembly, installation, commissioning (i.e., a boot, receiving inspection, delivery, transfer), setting (e.g., a set-up), teaching or programming or a switch of a process, operation, cleaning, detection of malfunctions (faults), and maintenance, as well as disassembly, disuse, and disposal when necessary.
Information for use shall includes the following:
● All information necessary to safely and properly use a machine in regard to the “intended use” of the machine;
● A notice or warning about residual risks. In addition, the necessity for training and protective equipment, and if necessary, the necessity for an additional guard and a protective device shall also be included; and
● A warning, etc. about risks resulting from an unintended use or a reasonably foreseeable misuse.
Give a warning about a hazardous event using a signal and an alarm device
An indicator light/flasher, or a buzzer/siren is used as a warning signal to indicate the condition of a machine. However, these signals need to meet the following conditions:
● They are given before a hazardous event occurs, and
● They are signals that are clearly recognizable.
In addition, these alarm devices need to be easily inspectable (if an inspection requires a lot of time and labor, regular inspections may be neglected).
In addition, attention is required to avoid a situation in which frequent activation results in workers ignoring or deactivating them.
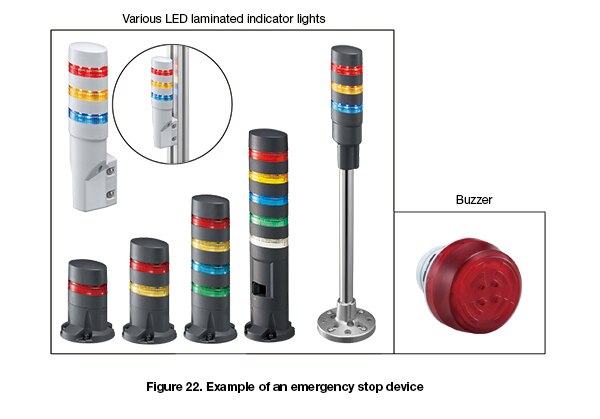
Display, warning message, and mark
- Name and address of the manufacturer, name of the product series, and production number (if any).
- Display of a mark of conformity with requirements (e.g., CE, UL marks).
- Various precaution / warning marks (rather than just write the word “danger,” describe what the danger is).
- It is desirable to preferentially use signs (pictographs) that can be recognized quicker than warning messages.
- Warning messages shall be written first in the language of a country in which the machine is used, and when required, in a language that an operator can understand
Accompanying documents (particularly, instructions handbook)
1. Information on the transport, handling, and storage of the machine
2. Information on the installation and commissioning (i.e., a boot, receiving inspection, delivery, transfer) of the machine
3. Information relating to the machine itself
4. Information on the use of the machine (e.g., the intended use, reasonably foreseeable misuse and prohibited matters, protective equipment to be used, and training)
5. Information on maintenance. This is, for example, presented by making a clear distinction between the following matters:
- Instructions on maintenance work that shall only be conducted by skilled personnel (i.e., maintenance personnel, specialized personnel); and
- Instructions on maintenance work that may be conducted by users (e.g., operators)
6. Information on disassembly, disuse, and disposal
7. Information on an emergency (e.g., operation methods at the time of a failure, a fire extinguisher)
Instructions for use
The requirements that apply to the preparation and presentation of instructions for use include the following:
1. The font and size of printed letters shall be the most legible ones. Warnings/precautions about safety shall be emphasized using colors, symbols, and/or large block letters; and
2. Information for use shall be written first in the language of a country in which the machine is used and in the first version. When multiple languages are used, it is desirable that each language should be easily distinguishable from the other ones, and the translation and the relevant diagram should be shown together.