One feature of this interlock switch is that no wear debris is generated because the actuator and sensor head do not come into physical contact. In addition, this interlock switch has no openings and few uneven surfaces, making it less susceptible to water and dust.
Non-contact safety switch | APAC
One feature of this interlock switch is that no wear debris is generated because the actuator and sensor head do not come into physical contact. In addition, this interlock switch has no openings and few uneven surfaces, making it less susceptible to water and dust.
Because the interlocking device can only be actuated by a certain combination, it is effective for preventing disabling by keys, coins, tools, and other objects.
IDEC offers two types of non-contact interlock switches that are equivalent to type 4.
One is a reed switch type non-contact interlock switch, and the other is an RFID type non-contact interlock switch (Figure 1, Figure 2).
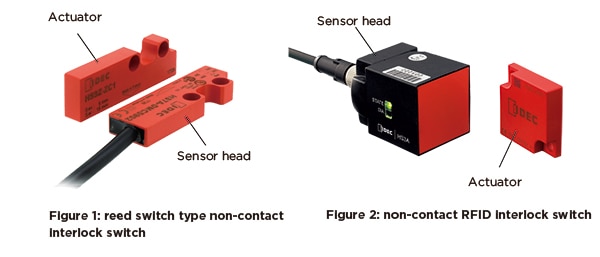
In addition to reliability, any non-contact interlock switch must also have the following features.
● Anti-tampering function
● Fault detection function. This is a function that stops the machine when it detects a fault and maintains the stop until the fault is resolved.
Reed Switch Type Non-contact Interlock Switches
Structure and Principles of Operation Actuation
The schematic structure of a reed switch type non-contact interlock switch is shown in Figure 3. It consists of a sensor head with multiple reed switches and a paired actuator with multiple magnets corresponding to the reed switches.
The sensor head is mounted on the machine, and the paired actuator is mounted on the door. Then, when the door is closed, the magnetic field near the sensor head becomes stronger, and the reed switch contacts are activated. When the door is opened, the magnetic field near the sensor head weakens, and the reed switch contacts return to their original state.
Anti-tampering Function
If there is only one pair of a magnet and reed switch, the contacts of the reed switch will be easily activated simply by bringing any commercially-available magnet, not an actuator, near it. For this reason, at least two pairs of magnets and reed switches are used, and the switch is determined to be “normal” only when all pairs are activated, which is a measure to prevent tampering by commercially-available magnets or other objects. The reed switch has an NO contact (normally open: open when the door is open) and an NC contact (normally closed: closed when the door is open), and both are used to prevent tampering by a wiring short circuit.
However, even if the above anti-tampering measures are taken, the possibility of tampering by a replacement actuator or an actuator removed from the door still remains. Therefore, a safety management system that includes measures to prevent the actuator from being removed from the door and management of replacement actuators is essential.
For more information, please visit the following link.
Fault Detection Function
Generally, reed switch type non-contact interlock switches are used in combination with a controller called a safety relay module. The main reason for this is that the contacts of the reed switch do not have a direct opening action function, and so a welded (A state where the contact surface melts and then cools and adheres due to an inrush current exceeding the capacity during contact opening and closing) contact could make it impossible to stop the machine. In order to detect this failure due to welded contacts, the combination of signals for the two reed switch circuits in the non-contact interlock switch must be monitored. If the controller detects a combination of signals that is not normal, it determines that a failure due to a welded contact has occurred and stops the safety output, thus stopping the machine. A schematic diagram of the concept is shown in Figure 4.
In this figure, we assume that one of the two circuits (reed switch B) has a welded contact. A function having a structure where the operating force of the actuator acts directly on the NC contact without the intervention of an elastic structural material (e.g., spring), and the NC contact opens when the actuator moves a predetermined distance. A state where the contact surface melts and then cools and adheres due to an inrush current exceeding the capacity during contact opening and closing.
Note that even if signals for two circuits are monitored, if the two circuits fail simultaneously, the simultaneous failure cannot be detected. Consequently, the reed switch has an NO contact (normally open: open when the door is open) and an NC contact (normally closed: closed when the door is open), and both are used to prevent a state where both switches fail simultaneously.
Features and Applications
As mentioned earlier, non-contact interlock switches do not generate wear debris because there is no physical contact.As a result, these switches are suitable for interlocking applications in cleanroom facilities for manufacturing semiconductors and their application products, which require a clean manufacturing environment.
In addition, the low surface roughness makes it difficult for foreign matter to adhere to or accumulate on the sensor head or actuator, and it is also used for interlock applications in food production equipment where it is essential to wash the entire equipment.
In general, non-contact interlock switches can be much smaller than mechanical interlock switches, and they can be placed in windows with a small turning radius as shown in Figure 5. This also allows a little more room for mounting accuracy compared to mechanical interlock switches.
Usage Notes
Because the actuator uses a magnet, if there are other magnets or ferromagnetic materials (steel plates) nearby, it must be placed at a distance where it will not be affected by them. Also avoid use of ferromagnetic materials for the screws that mount the sensor heads and actuators to machinery and equipment. Non-contact interlock switches cannot be used in environments where ferromagnetic metal powder such as iron powder is present in the surrounding environment.In addition, due to their characteristic of having no physical contact, non-contact interlock switches do not have a physical locking mechanism. Consequently, if the door needs to be physically locked, a separate locking mechanism such as a cylinder is required.
RFID Type Non-contact Interlock Switches
Structure and Principles of Operation
The schematic structure of an RFID type non-contact interlock switch is shown in Figure 6.When the actuator mounted to the door approaches the sensor head mounted to the machine, the RFID reader in the sensor head reads the ID data from the RFID in the actuator. This is checked against the ID that was already stored in the sensor head, and if it matches, the information that the door is closed is transmitted.
Anti-tampering Function
There are two types of RFID type anti-tampering functions: unicode type and multi-code type.● Unicode Type
This method transmits the information that the door is closed only when the RFID reader reads the specific RFID code that was paired at the start of operation (Figure 7). If an actuator that has not been paired is brought close to the door , the door will not be considered closed. This enables implementing of anti-tampering measures at an extremely high level. This is a method that maximizes the features of the RFID type. However, it is necessary to implement measures to prevent the paired actuator from being removed from the door.● Multi-code Type
This method transmits the information that the door is closed even if different actuators with the same RFID code are used. This method can also achieve a higher level of anti-tampering protection than the reed switch type. However, like the reed switch type, a safety management system that includes measures to prevent the actuator from being removed from the door and management of replacement actuators is essential.Fault Detection Function
Both unicode and multi-code types are capable of detecting faults by themselves by using the controller function (built-in IC and software) built into the sensor head.This means that an external controller for fault diagnosis is not required.
Conclusion
Table 2 shows a comparison of the anti-tampering and fault detection functions for the reed switch type and RFID type.
For anti-tampering functions, the mounting method and mounting location on the machine must also be taken into consideration. For more information, please visit the following link.